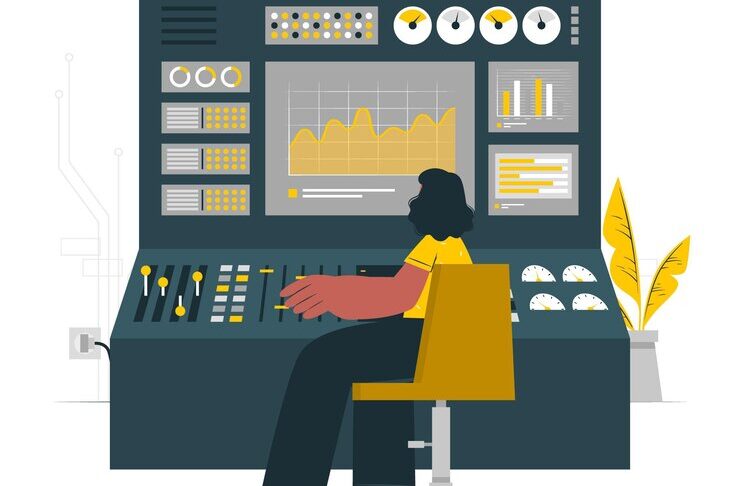
In the dynamic world of industrial automation, the Programmable Logic Controller (PLC) stands tall as a cornerstone technology, transforming the way industries manage processes and machinery. This blog delves into the pivotal role of motor control using PLCs for industrial applications, unraveling the multitude of advantages that have propelled PLCs to the forefront of modern automation.
Flexibility and Adaptability:
Programmable Logic Controllers are renowned for their unparalleled flexibility, making them the linchpin of adaptable industrial processes. In motor control applications, this flexibility translates to the ability to adapt to a wide array of tasks and processes. Whether it’s managing different motor types, adjusting speeds, or altering control strategies, PLCs provide a versatile platform that can be easily reprogrammed to meet evolving industrial requirements.
The adaptability of PLCs allows industries to respond swiftly to changing production needs. As new products are introduced or modifications are made to existing processes, PLCs can be reprogrammed without the need for extensive rewiring or system overhauls. This dynamic flexibility ensures that industries can remain agile and responsive in a rapidly evolving market.
Centralized Control:
Centralized control is a hallmark feature of PLCs, allowing for the efficient management of multiple motors within an industrial setup. This centralized approach streamlines the coordination of complex systems, facilitating synchronized operations and efficient communication between various components.
The benefits of centralized control extend beyond mere convenience. It enhances system reliability by minimizing the potential for discrepancies between different parts of the system. Troubleshooting and maintenance procedures become more straightforward, as operators can identify and address issues from a central control point, reducing downtime and optimizing overall system performance.
Ease of Programming:
Programming PLCs for motor control is inherently user-friendly, contributing to increased efficiency in project development. Engineers and technicians can employ graphical programming languages or ladder logic, which simplifies the development of intricate control algorithms. This ease of programming accelerates project timelines, reduces the likelihood of errors, and empowers the workforce to quickly adapt to changes in production requirements.
The user-friendly programming interface of PLCs is a significant advantage in industries where skilled programming personnel might be limited. The graphical representation of control logic allows operators to visualize and understand the system’s behavior, facilitating quicker and more accurate decision-making during the programming phase.
Real-Time Monitoring and Feedback:
PLCs offer real-time monitoring capabilities, providing instant feedback on the status and performance of motors. This real-time feedback is invaluable in ensuring that any deviations or anomalies can be promptly identified and addressed. The ability to monitor variables such as temperature, speed, and current allows for predictive maintenance, minimizing downtime and extending the lifespan of motors.
Real-time monitoring enhances the overall reliability of motor control systems by enabling proactive measures. Operators can set predetermined thresholds for key parameters, and if these thresholds are approached or breached, the PLC can trigger alarms or take corrective actions. This proactive approach minimizes the risk of unexpected failures and contributes to the overall efficiency and reliability of the industrial system.
Cost-Effectiveness:
Implementing PLC-based motor control systems often proves to be cost-effective in the long run. The initial investment in PLC technology is offset by reduced wiring, simpler control panel designs, and lower maintenance costs. Moreover, the scalability of PLC systems allows for gradual expansion and upgrades without requiring a complete overhaul of the existing infrastructure.
The cost-effectiveness of PLCs extends beyond the initial implementation phase. With simplified wiring and reduced hardware requirements, industries can achieve significant cost savings in terms of materials, labor, and space. Additionally, the ease of reprogramming PLCs facilitates swift adjustments to the control logic, reducing the need for extensive downtime during modifications or upgrades.
Integration with Other Control Systems:
PLCs seamlessly integrate with other control systems and devices, fostering a cohesive and interconnected industrial ecosystem. From Human Machine Interface (HMI) panels to sensors and actuators, PLCs serve as the backbone that harmonizes the entire control network. This integration capability is particularly valuable in industries where multiple processes need to work in tandem.
The ability of PLCs to communicate with various devices and control systems ensures a unified and synchronized operation. This integration is crucial for industries with complex automation needs, where different components must work in harmony to achieve overall system objectives. The interoperability of PLCs simplifies the integration process and enhances the overall efficiency of industrial control systems.
High-Speed Processing:
Motor control applications often demand rapid and precise responses. PLCs, designed for high-speed processing, excel in meeting these demands. With fast scan times and the ability to execute complex control algorithms swiftly, PLCs ensure that motor actions align seamlessly with the dynamic requirements of industrial processes.
The high-speed processing capabilities of PLCs are especially critical in applications where quick and precise motor control is paramount. Industries such as robotics, manufacturing, and material handling rely on PLCs to execute control logic with millisecond precision, ensuring that motors respond promptly to changing conditions and maintain optimal performance.
Reliability and Robustness:
Industrial environments are known for their harsh conditions, including temperature variations, humidity, and electromagnetic interference. PLCs are built to withstand these challenges, providing a robust and reliable platform for motor control. Their rugged design ensures consistent performance, contributing to the longevity of the entire control system.
The robustness of PLCs makes them well-suited for deployment in challenging industrial settings. Whether located in manufacturing plants, chemical processing facilities, or outdoor environments, PLCs can withstand the rigors of industrial operations. This reliability translates to increased uptime, reduced maintenance costs, and enhanced overall system dependability.
Remote Monitoring and Control:
PLCs equipped with remote connectivity capabilities enable operators and engineers to monitor and control motor-driven processes from a distance. This is particularly valuable in scenarios where on-site access is limited or for applications that require real-time adjustments without physical intervention. Remote monitoring enhances operational efficiency and reduces response times to potential issues.
The ability to monitor and control motor systems remotely provides a considerable advantage in industries with distributed operations or expansive facilities. Operators can access real-time data, diagnose issues, and implement corrective measures without the need for on-site presence. This capability streamlines maintenance efforts, reduces travel costs, and ensures rapid responses to emerging issues.
Comprehensive Diagnostics and Troubleshooting:
PLCs offer advanced diagnostic features that facilitate efficient troubleshooting. With detailed error logs, diagnostic messages, and alarms, engineers can quickly pinpoint issues, minimizing downtime. The comprehensive diagnostic capabilities of PLCs contribute to a proactive maintenance approach, ensuring the continued reliability of motor control systems.
Diagnostics play a pivotal role in maintaining the health of industrial systems. The ability of PLCs to provide detailed information about the state of motors, sensors, and other components allows engineers to identify potential issues before they escalate. This proactive approach to diagnostics reduces unplanned downtime, improves system reliability, and ultimately extends the lifespan of industrial equipment.
Conclusion:
In conclusion, the adoption of PLCs for motor control in industrial applications brings forth a multitude of advantages that significantly enhance efficiency, reliability, and adaptability. The flexibility of PLCs, coupled with their centralized control capabilities, ease of programming, and real-time monitoring, positions them as a cornerstone in modern industrial automation.
As industries continue to evolve, embracing PLC technology for motor control not only meets the current demands of efficiency but also provides a scalable and future-ready solution for the dynamic landscape of industrial automation. The advantages outlined above collectively contribute to a transformative impact on industrial processes, offering a paradigm shift towards smarter, more efficient, and responsive motor control systems.
As we look ahead, the role of PLCs in motor control is poised to grow even more significant. The ongoing advancements in PLC technology, such as the integration of Artificial Intelligence (AI) and Internet of Things (IoT) capabilities, promise to further enhance the capabilities of motor control systems. These innovations open up new possibilities for predictive maintenance, energy optimization, and adaptive control strategies.
In conclusion, the utilization of PLCs for motor control in industrial applications represents a symbiotic relationship between technology and efficiency. The advantages of flexibility, centralized control, ease of programming, real-time monitoring, cost-effectiveness, integration capabilities, high-speed processing, reliability, remote accessibility, and comprehensive diagnostics collectively position PLCs as the linchpin of modern industrial automation.
The transformative impact of PLC-based motor control extends beyond immediate operational benefits. It lays the foundation for sustainable, adaptive, and future-proof industrial processes. Embracing PLC technology is not merely an investment in the present but a strategic move towards building resilient, efficient, and agile industrial ecosystems that can thrive in the face of ever-evolving challenges. As industries navigate the complexities of a dynamic global landscape, PLCs continue to be the driving force behind the pursuit of excellence in motor control and industrial automation.