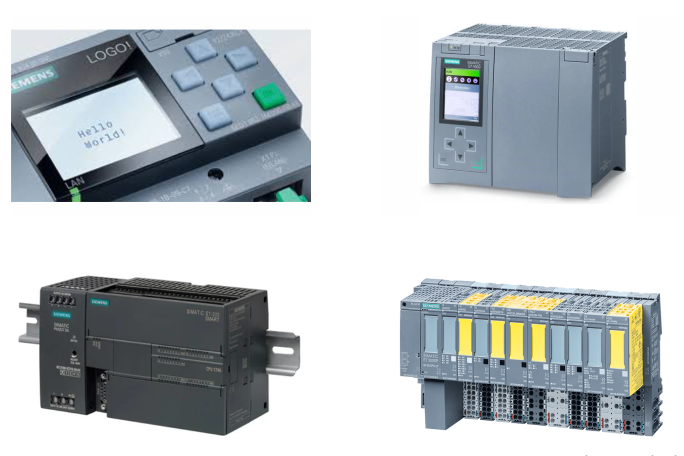
In today’s rapidly advancing world, automation is everywhere. From factories to household appliances, automation helps make our lives easier and more efficient. At the heart of many automation systems is something called a “PLC motors.” If you’re unfamiliar with this term, don’t worry. In this blog, we will explore what a PLC motor is, how it works, and why it’s so essential in the world of automation.
What is a PLC?
Before we dive into the details of PLC motors, let’s first understand what a PLC is. PLC stands for Programmable Logic Controller. It’s a high-tech computer designed specifically for industrial automation tasks. A PLC can be programmed to perform specific tasks, such as controlling machines, monitoring processes, or even managing safety systems.
PLCs are designed to withstand tough environments, like those found in factories. They can handle extreme temperatures, vibrations, and even electrical noise. This makes them ideal for use in heavy industries such as manufacturing, mining, and oil and gas.
What is a PLC Motor?
Now that we know what a PLC is, let’s talk about PLC motors. Simply put, a PLC motor is a motor that is controlled by a PLC. The PLC sends signals to the motor to control its speed, direction, and position. This allows the motor to perform specific actions, like rotating a conveyor belt, operating a robotic arm, or controlling a valve.
The combination of PLCs and motors is powerful because it allows machines to operate precisely and efficiently. The PLC can monitor the motor’s performance and make adjustments in real-time. This level of control is essential for industries where accuracy and reliability are crucial.
How Does a PLC Motor Work?
The process of how a PLC motor works might seem complicated, but it can be broken down into simple steps:
Input Signals: A PLC receives input signals from sensors or human operators. These inputs can include things like a start button being pressed, a sensor detecting an object, or a temperature reading.
Processing: The PLC processes these inputs based on its programmed instructions. For example, if a sensor detects an object on a conveyor belt, the PLC might be programmed to start the motor and move the belt.
Output Signals: Once the PLC has processed the inputs, it sends output signals to the motor. These signals tell the motor to start, stop, speed up, or slow down.
Motor Action: The motor then performs the action based on the signals it receives. If the PLC tells the motor to rotate at a certain speed, it will do so. If it needs to stop or change direction, the motor will respond accordingly.
Feedback Loop: In many cases, PLC motors are part of a feedback loop. This means that the motor sends information back to the PLC about its current status. The PLC can use this information to make further adjustments, ensuring smooth and accurate operation.
Types of PLC Motors
There are several different types of motors that can be controlled by a PLC. The choice of motor depends on the specific application and the level of control required. Some common types include:
AC motors, driven by Alternating Current (AC), are extensively employed across various industrial settings. They are reliable, efficient, and can handle high power loads. PLCs can control the speed and direction of AC motors using variable frequency drives (VFDs).
DC Motors: Direct Current (DC) motors are often used in applications where precise control is required. PLCs can easily adjust the speed and direction of DC motors, making them ideal for tasks that require high precision.
Stepper Motors: Stepper motors are designed to move in small, precise steps. They are often used in applications like 3D printers or CNC machines. PLCs can control the position and speed of stepper motors with great accuracy.
Servo Motors: Servo motors are similar to stepper motors but offer even more precise control. They are often used in robotics and other applications where accuracy is critical. A PLC can control the exact position, speed, and torque of a servo motor.
Applications of PLC Motors
PLC motors are used in a wide range of industries and applications. Some of the most common uses include:
Manufacturing: In factories, PLC motors are used to control conveyor belts, robotic arms, and other machinery. This helps increase efficiency, reduce waste, and improve product quality.
Automotive: In the automotive industry, PLC motors are used in assembly lines to control various machines and robots. They help automate tasks like welding, painting, and assembling car parts.
Food and Beverage: In the food and beverage industry, PLC motors are used to control packaging machines, mixers, and ovens. They ensure that products are processed and packaged efficiently and consistently.
Energy: In the energy sector, PLC motors are used to control turbines, pumps, and other equipment in power plants. They help ensure the safe and efficient operation of these critical systems.
Water Treatment: In water treatment plants, PLC motors control pumps, valves, and other equipment that manage the flow of water. They help ensure that clean water is delivered to homes and businesses.
Conclusion
PLC motors play a crucial role in modern automation. By combining the power of programmable logic controllers with the precision of motors, industries can achieve greater efficiency, reliability, and accuracy. Whether it’s controlling a simple conveyor belt or managing a complex robotic system, PLC motors are at the heart of many industrial processes.